鋁合金的特性來選擇切削液由于鋁合金強度和硬度相對較低,塑性較小,對刀具磨損小,且熱導率較高,使切削溫度較低,所以鋁合金的切削加工性較好,屬于易加工材料,切削速度較高,適于高速切削.但鋁合金熔點較低,溫度升高后塑性增大,在高溫高壓作用下,切削界面摩擦力很大。容易粘刀;特別是退火狀態(tài)的鋁合金,不易獲得低的表面粗糙度。
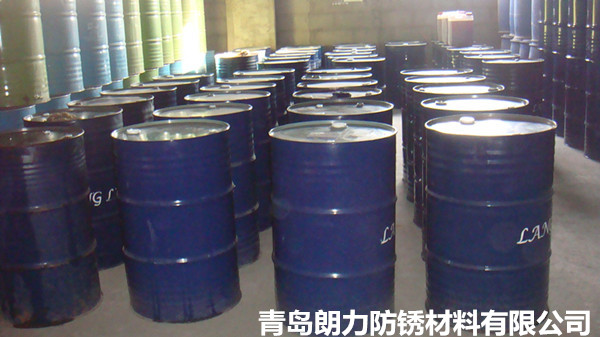
鋁合金的特性來選擇切削液2與鋼材和黃銅相比,鋁合金的特點,一是材質(zhì)軟,剛性差,二是彈性模量低,這兩個因素顯著影響了鋁合金的切削加工性。因此,在加工鋁合金工件時,必須充分地夾緊和支撐工件,并保持刀具鋒利;否則,工件往往會有離開切削刀具的傾向。有時工件的表面出現(xiàn)不規(guī)則的槽痕和光亮的擠壓斑,一種可能是由于刀具對工件的壓力不正常引發(fā)的,還有一種可能是由于夾持不牢固而引起振顫時,刀具在工件的表面作間隙式的磨蹭,發(fā)生擠壓現(xiàn)象和粉狀切削;然后,當間隙或彈性消失時,刀具就咬人工件的表面,啃出槽痕。
3為了獲得光潔的工件表面,盡可能采用粗切削和精切削的組合,因為各種合格的工件毛坯總會有一些氧化層,致使刀具受到相當程度的磨損。如果最后切削工序采用拋光過的鋒利刀具進行精細切削,就能達到以上要求。
4通常把鋁合金的切削性分為兩類:1類是指工業(yè)純鋁和硬度小于80HB的退火狀態(tài)鋁合金;2類是指淬火時效狀態(tài)的變形鋁合金。而鋁合金的切削加工工藝參數(shù)與此類別有關。
如何選擇合適的切削液
1硫化切削油與鋁形成強度高于鋁本身的硫化物,不但不能起到潤滑作用,反而會增大刀和屑接口間的摩擦。另外,切削鋁時用含氯的切削液也會產(chǎn)生類似的作用,因此切削鋁時不宜用硫化切削油以及含氯的切削液。
2一般來說,切削液要根據(jù)金屬的加工藝和要求來選擇。根據(jù)大多數(shù)經(jīng)驗來說,如果鋁切機鋸片為高速的鋼質(zhì)刀片進行低速切割時,我們推薦使用油性切削液,如果使用硬質(zhì)合金進行高速切割時,我們推薦使用水溶性切削液。
3總之,要根據(jù)具體切削加工條件及要求,根據(jù)純油性金屬切削液和水溶性金屬切削液的不同特點,同時考慮各個工廠的不同實際情況,如車間的通風條件、廢液處理能力及前后道工序的切削液使用情況等,來選取具體的切削液類型。